Adding recycled product to inventory.
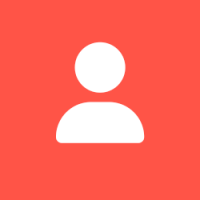

Hi Everyone, I wonder if there is anyone that could give a hand coming to grips with the following.
My company buys a liquid A in bulk. The product is treated as an inventory Item bought through the Reckon purchasing section and on receipt on site added to inventory. Product A is decanted on site into 20 ltr and 60 ltr containers, A20 and A60. As the price /ltr is lower for the higher quantity I have set up these items A20 and A60 as assembly items. As the 20ltr and 60 ltr containers are filled a docket goes to the office and the assemblies are built in Reckon.As the items A20 and A60 are sold and invoiced inventory is adjusted by the system.
Some of the product is returned to the site contaminated, amount is recorded (at present in a notebook). Once a reasonable volume is built up the contaminated product is reprocessed and is added to the inventory through a manipulation with a ghost company called DIST set up in the system. The product is purchased from DIST at a price equal to the processing cost of the product. The office goes through a process of raising a P.O. receiving and paying the bill.
This process gives us what we believe is an accurate indication of the cost of goods sold as it combines the cost of new product and reprocessed product. (it is a rather cumbersome process though)
I need to enhance the system further by adding the contaminated fluid returned from the customers to Reckon inventory ( as the product is hazardous tracking the product is a legal requirement). I am reluctant to introduce another purchasing/ receipting/billing procedure.
My question : Can anyone suggest a process to use which allows me to enter contaminated product as say product B and converting this product into product A while adding the cost of conversion to product A.
Thanks,
Jack
Te Puke
Comments
-
Hello Jack,
I can see what you are doing with the product in the real world but as to how to deal with it in the financial realm is a bit over my level of experience. Obviously the contaminated product would need to be assigned a different product code and purchase price from the supplier and then sold in 20L and 60L containers with a price per litre. Then you would need a discounted price for the recycled product using a form of depreciation accounting.
Keeping control of the quantity in the bulk containers, the 20L and 60L decanted containers and the recycled product returned from the purchaser, and I gather gets filtered and restored for resale is a bit tricky but maybe somebody else reading this might have a Ureka moment and come up with a solution for you. The fact that it is a hazardous product would require the tightest of controls for handling it at all stages which could involve some added costs. I'll hand it on to someone else now for further answers. Good luck.
Robert Smeallie0